
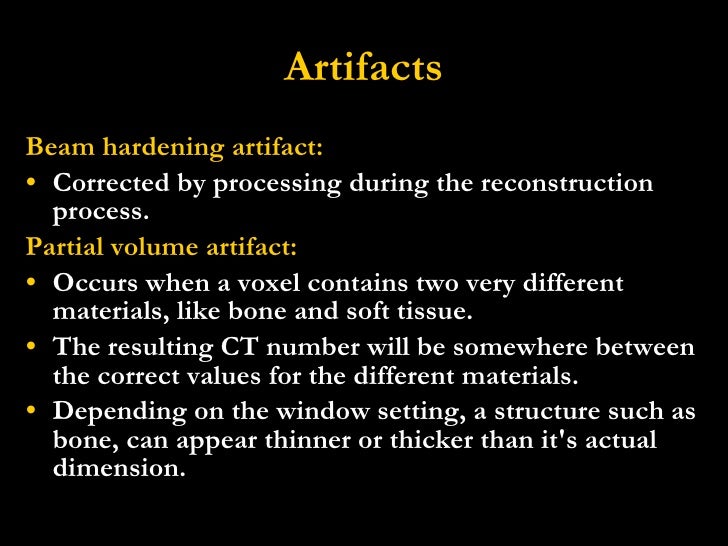
The acquired data cube consists of a stack of surface temperature images taken at different times. more » Pulsed thermography (PT) system utilizes a high intensity flash lamp to rapidly heat surface of sample, and a high sensitivity fast-frame megapixel infrared (IR) camera to capture data of surface temperature variations. As a solution to NDE of AM, we are developing pulsed thermal imaging which is non-contact, one-sided, and scalable to arbitrary size and shape of the AM parts. Currently, limited options are available for nondestructive evaluation (NDE), either during or post manufacturing. Known material flaws in AM include low-density regions consisting of non-sintered powder, which have to be detected to ensure the safety of long-term performance nuclear reactor components. « lessĪdditive manufacturing (AM, or 3D printing) for commercial nuclear energy applications is an emerging method for cost-efficient manufacturing aimed at replacing aging nuclear reactor parts and reducing costs for new construction. The direct-ED image has the potential to assist in more accurate organ contouring, and is a better fit for the desired purpose of CT simulations for radiotherapy. Conclusions: The low SDs on direct-ED images and relative consistent NPS values in the low spatial frequency domain indicate a reduction of beam-hardening artifacts. This also confirms the beam -hardening artifact reduction on ED images. Interestingly, the local NPS calculated from direct-ED images shows consistent values in the low spatial frequency domain for images acquired from all tube potential settings, while varied dramatically on HU images. Compared to that on HU images, the SDs are lower on direct-ED images, and the differences are up to 26%. The mean value differences between HU and direct-ED images are up to 8% with absolute value of 2.9. Results: Along with the increase of tube potentials, ROI means and SDs decrease on both HU and direct-ED images. A complete analysis of beam-hardening artifact reduction and image quality improvement was conducted. From these images, mean, standard deviation (SD), and local NPS were calculated for regions of interest (ROI) of same locations and sizes. Methods: HU and direct-ED images were reconstructed on a head phantom scanned on a Siemens Definition AS CT scanner at five more » tube potentials of 70kV, 80kV, 100kV, 120kV and 140kV respectively. This study is to quantitatively analyze the reduction of beam-hardening artifacts on direct-ED images and suggest additional clinical usages. An added benefit is that beam-hardening artifacts are also reduced on direct-ED images due to the underlying material decomposition. This feature can eliminate the need for kV specific calibration curve for radiation treatemnt planning. Purpose: A prototype reconstruction algorithm that can provide direct electron density (ED) images from single energy CT scans is being currently developed by Siemens Healthcare GmbH. A CT technique with higher kVp in combination with lower mAs is recommended when low-dose CT images are used for AC to minimize beam-hardening artifacts. = ∼ 4 μGy), the low dose limit for the CT exam as part of SPECT/CT will be guided by CT image quality requirements for anatomical localization and artifact reduction. We also present promising preliminary results of applying the deep networks trained using CAD models to experimental data obtained from XCT of an AM jet-engine more » turbine blade.
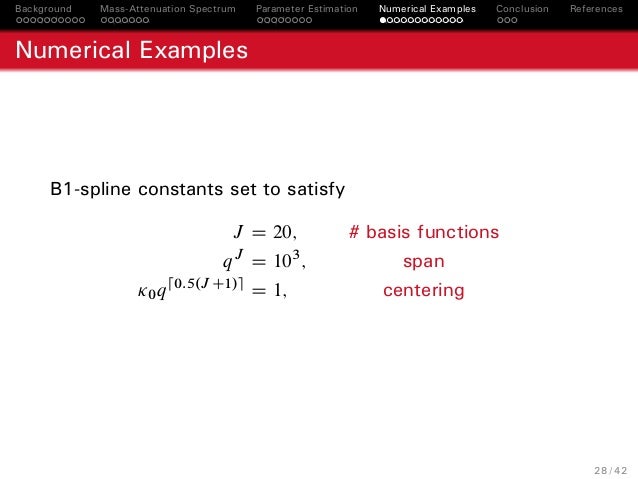
Using extensive experiments with simulated data sets, we demonstrate that our method can significantly improve the reconstruction quality, thereby enabling better detection of defects compared with the state of the art. In this work, we propose a novel framework based on using available computer-aided design (CAD) models for parts to be manufactured, accurate XCT simulations, and a deep-neural network to produce high-quality XCT reconstructions from data that are affected by noise and beam hardening. However, XCT of metal AM parts can be challenging because of artifacts produced by standard reconstruction algorithms as a result of a confounding effect called “beam hardening.” Beam hardening artifacts complicate the analysis of XCT images and adversely impact the process of detecting defects, such as pores and cracks, which is key to ensuring the quality of the parts being printed. X-ray computed tomography (XCT) has played a critical role in rapid NDE and characterization of AM parts. Nondestructive evaluation (NDE) of additively manufactured (AM) parts is important for understanding the impacts of various process parameters and qualifying the built part.
